技術紹介vlog/津田製作所60周年記念テープカッター1
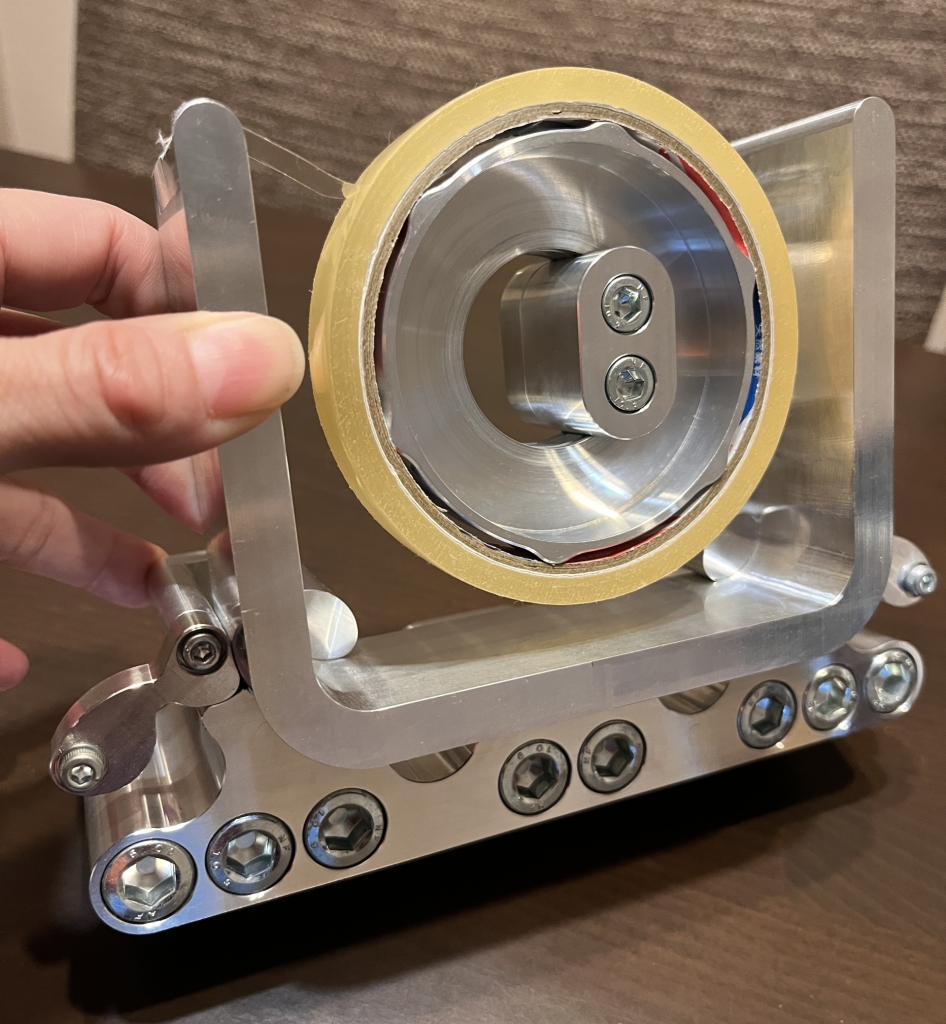
以前、60周年の記念品として自主製作したテープカッターについて書いたことがあります。
通常、車やオートバイ、船外機等の部品を作っている当社です。
テープカッターという初めてのジャンルで、本体まで全てを製品として製作するというものづくりは、
順調にいかないことも多々ありました。
得意分野の技術はどう取り入れたのか、
また、工夫した点や、難しかった点などもご紹介します!
一連のきっかけや心情は、全4回の過去ブログをご覧ください。
自主製作プロジェクトへの挑戦(1)【津田製作所60周年記念】
自主製作プロジェクトへの挑戦(2)【津田製作所60周年記念】
自主製作プロジェクトへの挑戦(3)【津田製作所60周年記念】
自主製作プロジェクトへの挑戦(4)【津田製作所60周年記念】
①加工
削り出しによる、全構造部品の一体化
素材:アルミブロック材(A5052)
加工方法:社内保有の5軸マシニングセンタを中心とした設備で全パーツを切削加工
鋳造・板金・溶接は一切使用せず、寸法公差・仕上がり品質・意匠性すべてを加工目も考慮した「削り」で実現
繋ぎ目をなくしたゆえの美しさを大切にしました。
カッター刃部の最適化と切れ味への工夫
このテープカッターの刃部が通常と違う点は、
刃部が本体と一体となっているところです。
開発は単なる外観再現ではなく、実用性を追求する工程でした。
最初は単純に、ギザギザを切削で均等に再現しましたが、
テープが伸びるだけで全く切れません。
そこで市販のテープカッターを分解・観察したところ、
「刃の角度」だけでなく、「刃に当たる前にテープが一度乗る面」が重要であることに気づきました。
その構造を再現するため、数種類の形状を試作し、加工角度やテープ当たりの高さを検証。
何度も切削条件と形状を見直し、現在の「しっかりとテープが切れる」形状にたどり着きました。
実際に使ってもらえることを目指した記念品であるからこそ、
切れ味という基本性能にも徹底してこだわりました。

②設計
重量設計と重心バランスの工夫
当初テープカッターは本体のみの予定でした。
しかし、滑り止めのついた本体を机に置いてテープを引っ張ったところ、
重量不足で本体も引っ張られて動いてしまったのです。
実は、事前にその心配の声はあったため、
それなりにバランスを考えて設計し、「これならいける!」と思ったものでしたが、
ここで今回1番の壁に当たってしまいます。
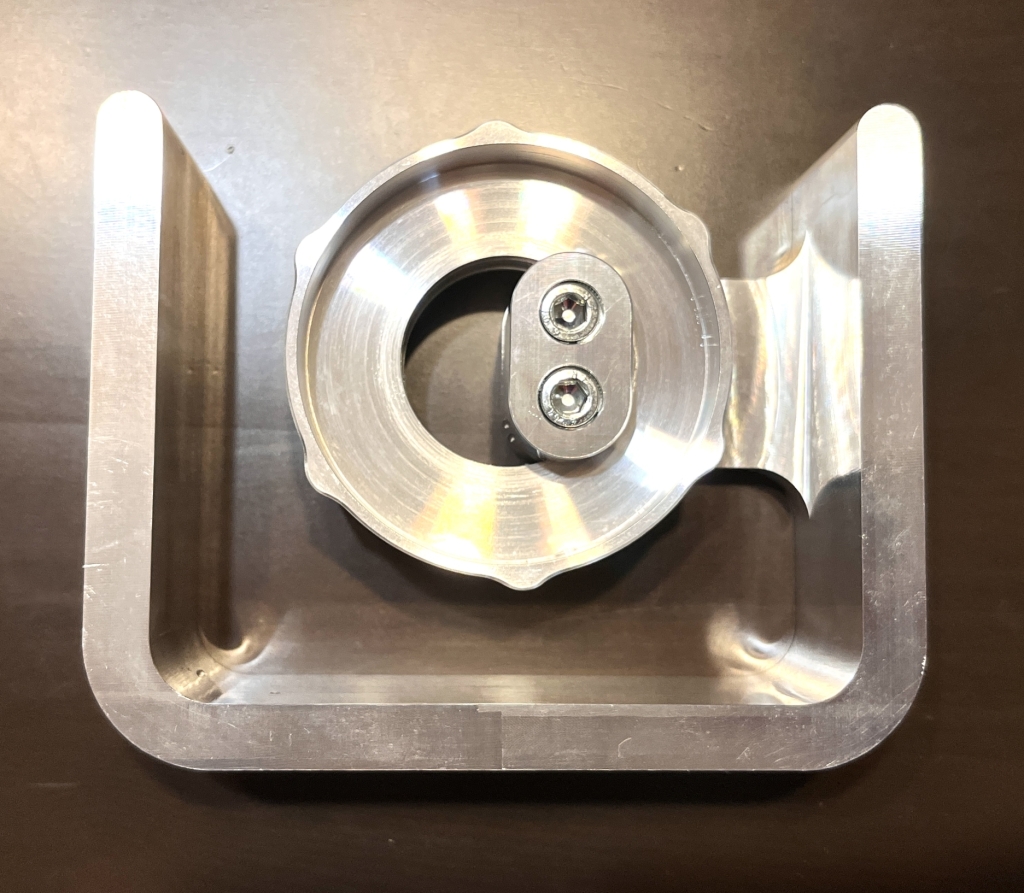
この問題の解決策として、
試行錯誤した形状と構造、デザインは大きく変えることなく、
本体とは別に、重量を補うための"着脱式ベース"を追加で設計しました。
そのベースの内部にスチールボルトを16本埋設することで、
外観の意匠性を損なわず、約1.5kgという理想的な総重量を確保し、加工性と重心位置を両立。
これは、ちょっと遊び心をくすぐる合体構造でありながら、
本体単体は手で持ってどこでも使用でき、土台と合体させた時には安定して片手で使用できるという、
汎用性も高まる結果となりました。
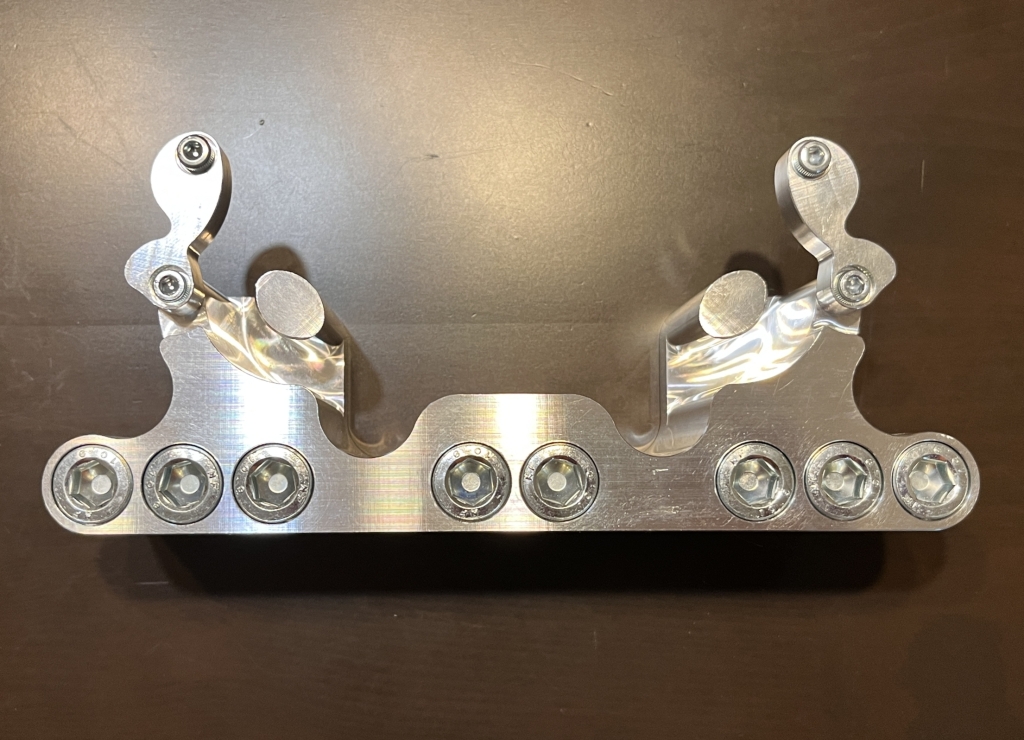
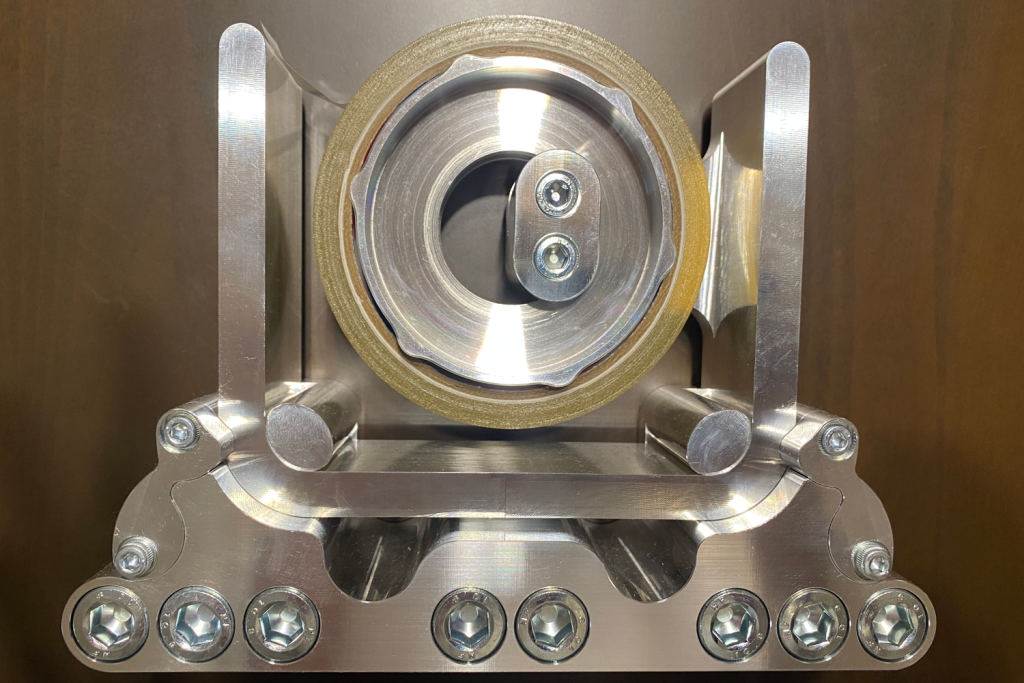
“中心軸を持たない“ホイール支持構造”
おそらくこのホイールの構造は世界に一つしかないと自負していますが、
テープ支持部を側面2本のボルトで浮かせながら保持し、同時に回転ガイドとする構造の設計です。
回転性能と摩耗対策のため、支持面の摩擦係数とクリアランスを細かく調整しながら、試作を複数回繰り返しました。
実物を見ていただくと、「どうしてこれでテープが回転するのか」と、
考えれば考えるほど不思議に思えてきます。
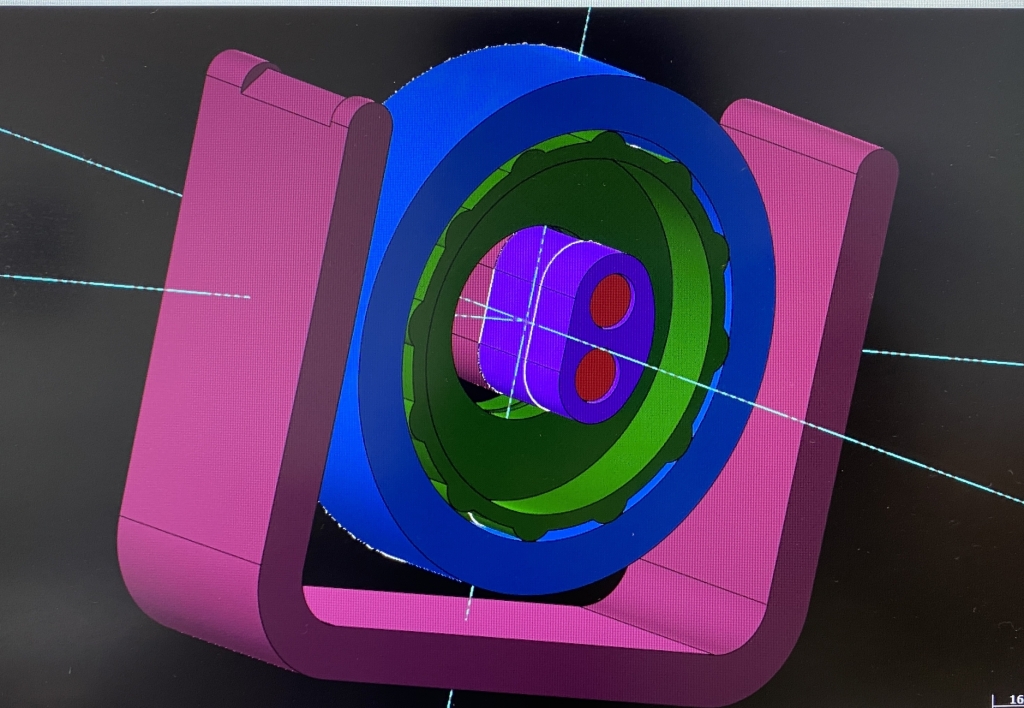
“圧力検査技術”を応用した、高精度滑り止め構造
当社で日常的に行っている漏洩試験・加圧試験での高精度Oリング溝加工技術を応用しました。
本体底面に嵌め込む滑り止めゴムの精密溝加工により、
机上での安定性と長期使用時の耐久性を確保しています。
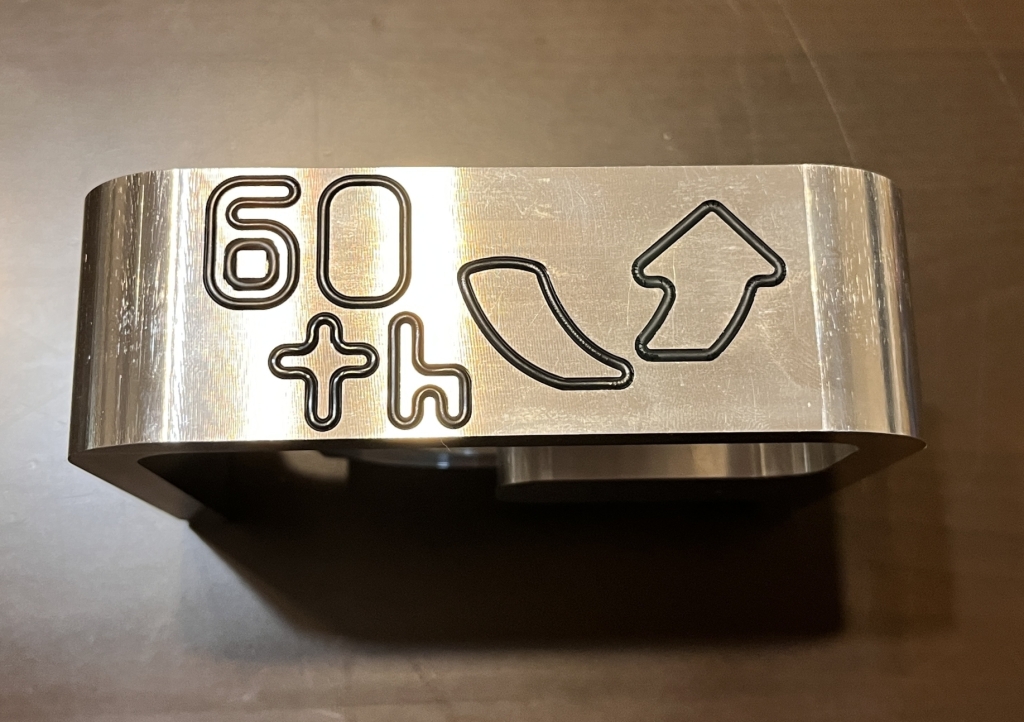
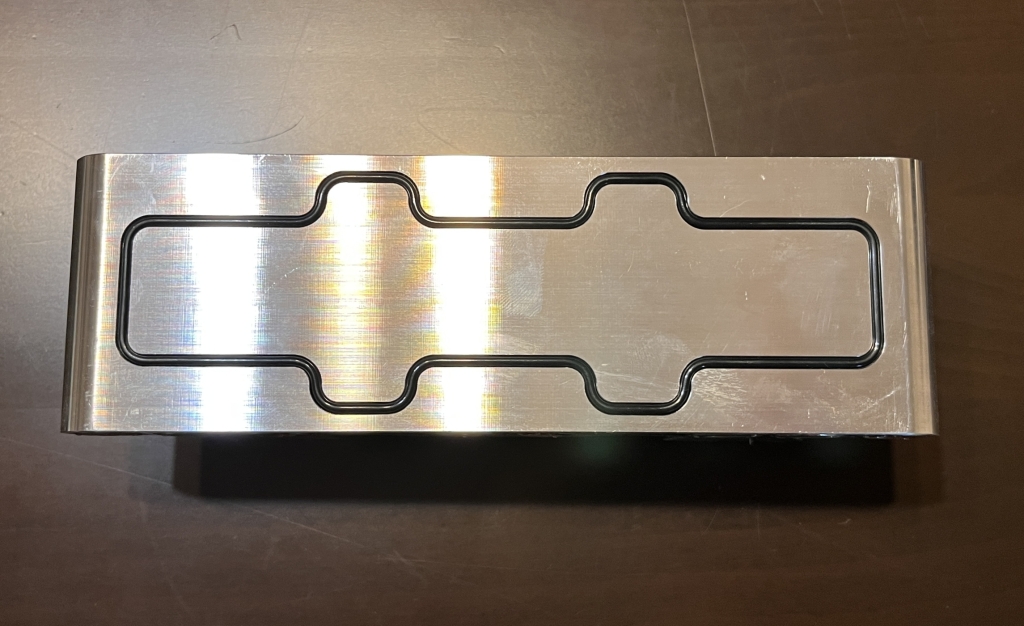
こうして出来上がった試作品をあれこれ改善するべく、さらに工夫を凝らしていくのですが、
長くなったので次回で書いていこうと思います。
#津田製作所 #金属切削加工 #試作 #開発 #広島 #精密部品 #ものづくり #プロジェクト